Revamping the Supply Chain - The Ashok Leyland Way

|
|
ICMR HOME | Case Studies Collection
Case Details:
Case Code : OPER004
Case Length : 08 Pages
Period : 1992-1998
Organization : Ashok Leyland
Pub Date : 2002
Teaching Note : Available
Countries : India
Industry : Automobiles
To download Revamping the Supply Chain - The Ashok Leyland Way case study (Case Code: OPER004)
click on the button below, and select the case from the list of available cases:
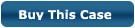
Price:
For delivery in electronic format: Rs. 200; For delivery through courier (within India): Rs. 200 + Rs. 25 for Shipping & Handling Charges
» Operations Case Studies
» Case Studies Collection
» ICMR HOME
» View Detailed Pricing Info
» How To Order This Case » Business Case Studies » Case Studies by Area
» Case Studies by Industry
» Case Studies by Company
Please note:
This case study was compiled from published sources, and is intended to be used as a basis for class discussion. It is not intended to illustrate either effective or ineffective handling of a management situation. Nor is it a primary information source.
|
<< Previous
'Together We Can'-Beat the Recession
AL did not seem to succumb to the 'uncertainty gloom' that was playing havoc to
its business environment. It decided to meet the challenge by re-gearing its
systems, be it material order, procurement, material handling, inventory control
or production. AL conducted brainstorming sessions inviting ideas on cost
cutting. Quality Circle teams were formed for this purpose. Said Thomas T.
Abraham, deputy general manager, Corporate Communications, "Our Quality Circle
teams were very helpful at this juncture and the worker involvement made it
easier to address cost cutting." AL took every employee's ideas into account and
figured out a way to keep things going and reduce production without inflicting
pain.
|
|
The recession saw AL waging a war on wastage and inefficiency. AL took many
initiatives ranging from tiering its vendor network to reducing the number
of vendors, and consequently, moving to a just-in-time (J-I-T) ordering
system, to joint-improvement programmes (JIP), which were essentially
exercises in value-engineering undertaken in association with key vendors.
|
It set up
different tier-levels to improve the quality of the suppliers. Tiering
formed the basis of the vendor-consolidation drive. Till 1998, Ashok
Leyland used to source the 62 components that went into its front-end
structure of its trucks and buses, from 16 suppliers.
In 2000, one tier-I vendor sourced the products from the other vendors
and supplied the assembly to the company. This saved cost and time
provided the vendor network was well coordinated with AL's own
manufacturing operations. At AL, Vendor Development and Strategic
Sourcing were handled by Corporate Materials Department (CMD). |
CMD identified the vendors, rated the vendors based on
feedback received from Supplier Quality Assurance Cell, send
drawings/specifications, called for quotes with detailed breakup of
operation-wise costs, and negotiated the price at which the parts would be
supplied. In addition to CMD, there were Materials Management Departments (MMDs)
for scheduling based on unit production plan...
Excerpts >>
|
|