General Motors: The CAD - CAM - CAE Journey

|
|
ICMR HOME | Case Studies Collection
Case Details:
Case Code : OPER017
Case Length : 13 Pages
Period : 1990 - 2002
Organization : General Motors
Pub Date : 2002
Teaching Note : Available
Countries : India
Industry : Automobiles Manufacturing
To download General Motors: The CAD - CAM - CAE Journey case study
(Case Code: OPER017) click on the button below, and select the case from the list of available cases:
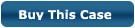
Price:
For delivery in electronic format: Rs.
500;
For delivery through courier (within India): Rs. 500 + Rs. 25 for Shipping & Handling Charges
» Operations Case Studies
» Case Studies Collection
» ICMR HOME
» View Detailed Pricing Info
» How To Order This Case » Business Case Studies » Case Studies by Area
» Case Studies by Industry
» Case Studies by Company
Please note:
This case study was compiled from published sources, and is intended to be used as a basis for class discussion. It is not intended to illustrate either effective or ineffective handling of a management situation. Nor is it a primary information source.
|
<< Previous
Introduction Contd...
Hughes Electronics Corp., GM Locomotive Group and Allison Transmission Division
were GM's major subsidiaries.
To facilitate growth across the world, GM had
strategic alliances with Fuji Heavy Industries Ltd., Suzuki Motor Corp., Fiat
Auto SpA and Isuzu Motors Ltd.
It also had vehicle ventures with Toyota Motor Corp. and Renault SA, and
technical collaborations with Toyota Motor Corp. and Honda Motor Co.. GM managed
to build a huge loyal customer base over the decades and went from strength to
strength, retaining its world leader crown (Refer Exhibit II for GM's
financials).
|
|
The first cars manufactured were constructed individually and a single
person assembled all the parts together. However, with the advent of the
conveyor-belt based assembly line technique in 1913-14 (at a Ford plant),
car manufacturing became much more efficient.
|
Under this
technique, a car moved along a belt as it was being built. Instead of
all workers working on a single car, they added parts to the car as it
moved along the belt. This made the manufacturing process faster and
cheaper.
GM also adopted the assembly line technique. The company had 160 plants
across the world and more than 300,000 employees. The manufacturing
process was categorized into powertrain1, metal fabrication and assembly
(Refer Table II). However, GM's cost of production in terms of time and
labor was more than any other automakers in the world. |
The company's internal problems had reportedly resulted in
the longest vehicle development process times, slow response to market trends
and 'dull products.' Toyota's (Japan) time-to-market was twice that of GM
throughout the 1980s and early 1990s. Ford Motor Co., which was half of GM in
size, was believed to be much more productive (Refer Figure I)...
Excerpts >>
|
|